By Eric Kadaj, Energy Recovery Senior Director of Market and Applications Development, and Erik Desormeaux, Energy Recovery Director of New Applications
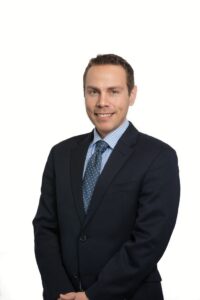
Eric Kadaj, Energy Recovery Senior Director of Market and Applications Development
Clean water is one of the world’s most precious resources. It is vital to our lives, and in many ways our livelihoods. Countless industrial enterprises that indirectly support many of our basic needs rely on water for their operations. In order to preserve our water supply, water producers, government agencies, and consumers need to consider the entirety of our water and waste systems in order to eliminate as much waste and inefficiency as possible. This is the concept behind a circular economy, which aims to make use of materials and resources for as long as possible.
In the context of water, a circular economy can turn wastewater into fresh water and other valuable resources such as minerals or nutrients. Several essential industries such as agriculture, battery production, and steel manufacturing produce useful resources as a byproduct, which are largely being wasted. By utilizing modern, advanced wastewater treatment and energy efficiency technology, it is now possible to take what we once considered waste and turn it into clean water, fertilizer, batteries, and more.
A Circular Water System
The core principle of a circular economy is reducing waste and building sustainable practices into every step of a product or resource’s production and use. In the water cycle, there are four main waypoints to consider:
- Consumption – By conserving water and reducing unnecessary consumption, we can reduce waste and preserve our current freshwater supply.
- Water Management – Wastewater treatment, both municipal and industrial, removes pollutants from contaminated water and, when treated properly with advanced technology, can produce a new supply of clean water. Regulations and environmental protections are key in achieving a high level of wastewater treatment and water reuse.
- Waste – Advanced wastewater treatment can produce clean water as well as a reduced volume of concentrated discharge. Depending on the source of the wastewater, this remaining discharge may contain valuable minerals or nutrients. Reverse osmosis (RO)-based resource recovery is a process that makes it possible to extract these minerals in order to reuse them and further eliminate “waste”.
- Production – Water reuse completes the cycle and incorporates water back into the supply.
Incorporating advanced treatment and recovery processes into the water system is often necessary to reduce waste and maximize reuse. However, these processes will inherently consume some resources. By utilizing energy efficient processes and technology such as energy recovery devices (ERDs) within RO systems, we can further reduce waste and minimize our environmental impact.
Lithium Battery Production
We are in a period of major global transition as the world moves away from its reliance on fossil fuels and towards electrification, which is a more sustainable alternative when powered by renewable electricity. Lithium batteries are critical to this transition, and we have seen a rapid increase in the demand for the many components involved in the production of rechargeable batteries including lithium iron phosphate (LFP) cathodes, which is the fastest growing type of battery cathodes for electric vehicles. The challenge here is that for every one ton of LFP produced, there is a nearly equivalent amount of waste created. This presents a major environmental challenge, which is why China – the main producer of LFP – requires many manufacturers to treat wastewater to the point of zero liquid discharge (ZLD). ZLD is a process where no water remains in the waste stream after treatment. The water is recaptured and reused in the process or safely discharged to the environment.
We partnered with the developer of a wastewater treatment facility servicing a manufacturer producing 50,000 tons per year of LFP cathodes in China to successfully implement a low energy, low cost ZLD treatment process that turned waste into clean water and ammonia sulfate, which can be sold for use as fertilizer. The treatment facility utilized both seawater reverse osmosis (SWRO) and ultra high-pressure reverse osmosis (UHPRO) to treat the wastewater to the point of ZLD. Our energy recovery devices – the PX® Pressure Exchanger® and the PX U Series – were installed in the SWRO and UHPRO stages to significantly reduce energy use, reducing the facility’s operating costs and environmental impact.
The PX and PX U Series both work by capturing wasted pressure energy and reintroducing it to the system at efficiencies exceeding 95%, which epitomizes the principle of a circular economy and provides both economic and sustainability benefits. In the case of this facility, introducing an effective wastewater treatment process allowed for 98% of the wastewater to be reused by the facility, reducing their overall water consumption. The use of energy recovery devices and production of ammonia sulfate as a byproduct also made this process cost effective for the LFP cathode manufacturer.
Steel Manufacturing and Metals Recovery
Nickel sulfate is another metal that has a large role to play in the transition to electrification. Currently, it is mainly used in the production of stainless steel, however, as the demand for lithium-ion batteries continues to grow, the demand for nickel will grow accordingly. Stainless steel manufacturing and battery recycling are both processes that use water and produce wastewater that contains nickel sulfate. This presents an opportunity to recover the nickel sulfate from the waste stream.
Combining the nickel sulfate recovery with a wastewater treatment process accomplishes two things: it produces a brine that has a higher concentration of nickel sulfate making the recovery process more effective, and it produces clean water that the manufacturer can reuse. Currently, thermal wastewater treatment is the dominant method, however, this is a very energy intensive process. Membrane-based treatment processes are much more energy efficient than thermal processes and allow for the use of energy recovery devices, such as Energy Recovery’s range of PX devices, to further reduce operating costs and emissions.
Nickel sulfate recovery offers a major opportunity for steel manufacturers and battery recyclers to create an additional revenue stream and prevent valuable resources from going to waste. We have partnered with another battery manufacturer in China to design an RO system with PX technology that has reduced the energy and costs to concentrate lithium, nickel sulfate and cobalt sulfate streams during their battery recycling process to recover these valuable materials for reuse.
Agriculture: Turning Manure into Revenue
Manure from livestock production when stored at volumes too large for local use presents a major hazard for the environment and a source of wastewater with valuable nutrients that typically go to waste. If properly treated, manure can be turned into useful biogas and fertilizer. Currently one of the predominant methods of disposing manure is to dump it into large ponds, which can overflow and leech into nearby land and water sources and contaminate them. When manure enters local water sources, it can also create algae blooms that disrupt the ecosystem and kill marine life on a wide scale.
But there is another way. A treatment facility in Greenleaf, Wisconsin processes nearly one million gallons of manure each day, representing the combined waste of over 35,000 cows from 11 dairy farms. Through a combination of digesters and advanced filtration processes, the manure is converted into biogas, concentrated nutrients that can be used as fertilizer, and over 400,000 gallons per day of clean water. The digesters heat up the manure and convert it into fuel, which can be sold as a byproduct, and solids, which are processed into fiber bedding that the farms can reuse for livestock. The digester process also uses water, and the resulting wastewater is processed further using filtration processes that include reverse osmosis. This process treats the water, separating it into concentrated nutrients for fertilizer and clean water, both of which can then be reused by the farm, resulting in a circular process that takes harmful waste and converts it into useful resources.
This project is a powerful model for the agriculture industry that demonstrates that sustainable processes can be beneficial in more ways than one. And just as in the LFP wastewater treatment facility, energy recovery devices, such as the Pressure Exchanger, can be introduced into the reverse osmosis stages in order to reduce energy consumption, costs, carbon emissions, and harness the valuable pressure energy within the system for reuse. We are partnering with Digested Organics, the designers of the advanced membrane processes at this facility, to implement PX technology into future fertilizer recovery systems to reduce cost and energy use while also improving system reliability.
Looking Ahead
By adopting the principles of a circular economy, manufacturers can not only reduce their impact on their environment, but also create opportunities to reduce their consumption, make their processes less resource intensive, and create an additional revenue stream. Critical minerals and metals like lithium, phosphorus, cobalt, and nickel are in limited supply in the world and demand is only expected to increase, presenting a prime opportunity for manufacturers to create value from their waste. For farmers, disposing of manure can either be a major burden or an opportunity. Circular thinking allows us to expand our perspective and consider whether wastewater truly is something to be wasted.